खराब जल प्रतिरोध, असमान सतह, उच्च पाउडर सामग्री, और असमान लंबाई?जलीय चारा उत्पादन में सामान्य समस्याएँ और सुधार के उपाय
जलीय चारे के हमारे दैनिक उत्पादन में, हमें विभिन्न पहलुओं से कुछ समस्याओं का सामना करना पड़ा है।यहां सभी के साथ चर्चा करने के लिए कुछ उदाहरण दिए गए हैं, जो इस प्रकार हैं:
1、 FORMULA
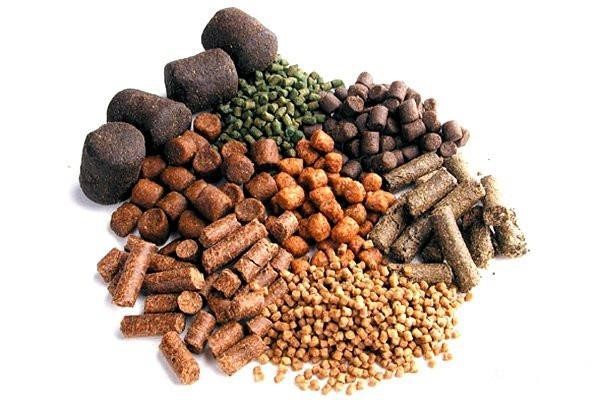
1. मछली फ़ीड की सूत्र संरचना में, अधिक प्रकार के भोजन कच्चे माल होते हैं, जैसे रेपसीड भोजन, कपास भोजन, आदि, जो कच्चे फाइबर से संबंधित होते हैं।कुछ तेल कारखानों में उन्नत तकनीक होती है, और तेल मूल रूप से बहुत कम सामग्री के साथ सूखा तला जाता है।इसके अलावा, इस प्रकार के कच्चे माल उत्पादन में आसानी से अवशोषित नहीं होते हैं, जिसका दानेदार बनाने पर बहुत अधिक प्रभाव पड़ता है।इसके अलावा, कपास के आटे को कुचलना मुश्किल होता है, जो दक्षता को प्रभावित करता है।
2. समाधान: रेपसीड केक का उपयोग बढ़ा दिया गया है, और चावल की भूसी जैसी उच्च गुणवत्ता वाली स्थानीय सामग्री को सूत्र में जोड़ा गया है।इसके अतिरिक्त, गेहूं, जो सूत्र का लगभग 5-8% है, जोड़ा गया है।समायोजन के माध्यम से, 2009 में दानेदार बनाने का प्रभाव अपेक्षाकृत आदर्श है, और प्रति टन उपज में भी वृद्धि हुई है।2.5 मिमी कण 8-9 टन के बीच हैं, जो पहले की तुलना में लगभग 2 टन की वृद्धि है।कणों की उपस्थिति में भी काफी सुधार हुआ है।
इसके अलावा, बिनौला खली को कुचलने की दक्षता में सुधार करने के लिए, हमने कुचलने से पहले बिनौला खली और रेपसीड खली को 2:1 के अनुपात में मिलाया।सुधार के बाद, कुचलने की गति मूलतः रेपसीड भोजन की कुचलने की गति के बराबर थी।
2、 कणों की असमान सतह
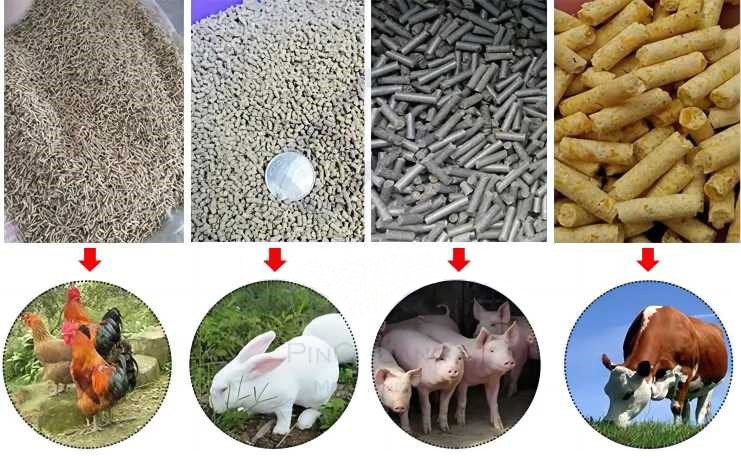
1. इसका तैयार उत्पाद की उपस्थिति पर बहुत प्रभाव पड़ता है, और जब इसे पानी में मिलाया जाता है, तो इसके ढहने का खतरा होता है और इसकी उपयोग दर कम होती है।मुख्य कारण यह है:
(1) कच्चे माल को बहुत मोटे तौर पर कुचल दिया जाता है, और तड़के की प्रक्रिया के दौरान, वे पूरी तरह से परिपक्व और नरम नहीं होते हैं, और मोल्ड छेद से गुजरने पर उन्हें अन्य कच्चे माल के साथ अच्छी तरह से जोड़ा नहीं जा सकता है।
(2) कच्चे फाइबर की उच्च सामग्री वाले मछली फ़ीड फार्मूले में, तड़के की प्रक्रिया के दौरान कच्चे माल में भाप के बुलबुले की उपस्थिति के कारण, कण संपीड़न के दौरान मोल्ड के अंदर और बाहर के बीच दबाव अंतर के कारण ये बुलबुले टूट जाते हैं, जिसके परिणामस्वरूप कणों की सतह असमान हो जाती है।
2. प्रबंधन के उपाय:
(1) क्रशिंग प्रक्रिया को ठीक से नियंत्रित करें
वर्तमान में, मछली फ़ीड का उत्पादन करते समय, हमारी कंपनी थोक कच्चे माल के रूप में 1.2 मिमी छलनी माइक्रो पाउडर का उपयोग करती है।हम कुचलने की सुंदरता सुनिश्चित करने के लिए छलनी के उपयोग की आवृत्ति और हथौड़े के घिसाव की मात्रा को नियंत्रित करते हैं।
(2) भाप के दबाव को नियंत्रित करें
सूत्र के अनुसार, उत्पादन के दौरान भाप के दबाव को यथोचित रूप से समायोजित करें, आम तौर पर 0.2 के आसपास नियंत्रित करें।मछली फ़ीड फार्मूले में मोटे फाइबर कच्चे माल की बड़ी मात्रा के कारण, उच्च गुणवत्ता वाली भाप और उचित तड़के की आवश्यकता होती है।
3、 कणों का खराब जल प्रतिरोध
1. इस प्रकार की समस्या हमारे दैनिक उत्पादन में सबसे आम है, जो आमतौर पर निम्नलिखित कारकों से संबंधित है:
(1) कम तड़के का समय और कम तड़के के तापमान के परिणामस्वरूप असमान या अपर्याप्त तड़का, कम पकने की डिग्री और अपर्याप्त नमी होती है।
(2) अपर्याप्त चिपकने वाली सामग्री जैसे स्टार्च।
(3) रिंग मोल्ड का संपीड़न अनुपात बहुत कम है।
(4) सूत्र में तेल की मात्रा और कच्चे फाइबर कच्चे माल का अनुपात बहुत अधिक है।
(5) क्रशिंग कण आकार कारक।
2. प्रबंधन के उपाय:
(1) भाप की गुणवत्ता में सुधार, नियामक के ब्लेड कोण को समायोजित करना, तड़के का समय बढ़ाना और कच्चे माल की नमी की मात्रा को उचित रूप से बढ़ाना।
(2) सूत्र को समायोजित करें, स्टार्च कच्चे माल को उचित रूप से बढ़ाएं, और वसा और कच्चे फाइबर कच्चे माल के अनुपात को कम करें।
(3) यदि आवश्यक हो तो चिपकने वाला जोड़ें।(सोडियम आधारित बेंटोनाइट घोल)
(4) के संपीड़न अनुपात में सुधार करेंअंगूठी मरो
(5) अच्छी तरह से कुचलने की सूक्ष्मता को नियंत्रित करें
4、 कणों में अत्यधिक पाउडर सामग्री
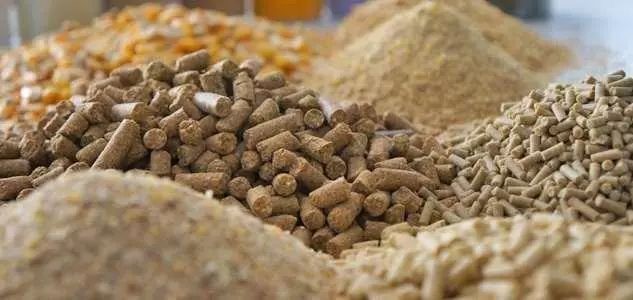
1. ठंडा करने के बाद और स्क्रीनिंग से पहले सामान्य पेलेट फ़ीड की उपस्थिति सुनिश्चित करना मुश्किल है।ग्राहकों ने बताया है कि छर्रों में अधिक महीन राख और पाउडर हैं।उपरोक्त विश्लेषण के आधार पर, मुझे लगता है कि इसके कई कारण हैं:
ए. कण की सतह चिकनी नहीं है, चीरा साफ नहीं है, और कण ढीले हैं और पाउडर उत्पादन का खतरा है;
बी. ग्रेडिंग स्क्रीन द्वारा अपूर्ण स्क्रीनिंग, बंद स्क्रीन जाल, रबर गेंदों का गंभीर घिसाव, बेमेल स्क्रीन जाल एपर्चर, आदि;
सी. तैयार उत्पाद के गोदाम में बहुत सारी महीन राख के अवशेष हैं, और निकासी पूरी तरह से नहीं है;
डी. पैकेजिंग और वजन के दौरान धूल हटाने में छिपे खतरे हैं;
निपटने के उपाय:
ए. सूत्र संरचना को अनुकूलित करें, उचित रूप से रिंग डाई का चयन करें, और संपीड़न अनुपात को अच्छी तरह से नियंत्रित करें।
बी. दानेदार बनाने की प्रक्रिया के दौरान, कच्चे माल को पूरी तरह से पकाने और नरम करने के लिए तड़के का समय, भोजन की मात्रा और दानेदार बनाने के तापमान को नियंत्रित करें।
सी. सुनिश्चित करें कि कण का क्रॉस-सेक्शन साफ-सुथरा है और स्टील स्ट्रिप से बने नरम काटने वाले चाकू का उपयोग करें।
डी. ग्रेडिंग स्क्रीन को समायोजित और बनाए रखें, और एक उचित स्क्रीन कॉन्फ़िगरेशन का उपयोग करें।
ई. तैयार उत्पाद गोदाम के तहत माध्यमिक स्क्रीनिंग तकनीक का उपयोग पाउडर सामग्री अनुपात को काफी कम कर सकता है।
एफ. तैयार उत्पाद गोदाम और सर्किट को समय पर साफ करना आवश्यक है।इसके अलावा, पैकेजिंग और धूल हटाने वाले उपकरण में सुधार करना आवश्यक है।धूल हटाने के लिए नकारात्मक दबाव का उपयोग करना सबसे अच्छा है, जो अधिक आदर्श है।विशेष रूप से पैकेजिंग प्रक्रिया के दौरान, पैकेजिंग कर्मचारी को नियमित रूप से पैकेजिंग स्केल के बफर हॉपर से धूल को खटखटाना और साफ करना चाहिए.
5、 कण की लंबाई भिन्न-भिन्न होती है
1. दैनिक उत्पादन में, हमें अक्सर नियंत्रण में कठिनाइयों का सामना करना पड़ता है, खासकर 420 से ऊपर के मॉडल के लिए। इसके कारणों को मोटे तौर पर इस प्रकार संक्षेप में प्रस्तुत किया गया है:
(1) दाने के लिए भोजन की मात्रा असमान है, और तड़के के प्रभाव में काफी उतार-चढ़ाव होता है।
(2) मोल्ड रोलर्स के बीच असंगत अंतर या रिंग मोल्ड और प्रेशर रोलर्स का गंभीर घिसाव।
(3) रिंग मोल्ड की अक्षीय दिशा के साथ, दोनों सिरों पर डिस्चार्ज गति बीच की तुलना में कम है।
(4) रिंग मोल्ड का दबाव कम करने वाला छेद बहुत बड़ा है, और खुलने की दर बहुत अधिक है।
(5) काटने वाले ब्लेड की स्थिति और कोण अनुचित है।
(6) दानेदार बनाने का तापमान।
(7) रिंग डाई कटिंग ब्लेड के प्रकार और प्रभावी ऊंचाई (ब्लेड की चौड़ाई, चौड़ाई) पर प्रभाव पड़ता है।
(8) साथ ही, संपीड़न कक्ष के अंदर कच्चे माल का वितरण असमान है।
2. फ़ीड और छर्रों की गुणवत्ता का विश्लेषण आम तौर पर उनके आंतरिक और बाहरी गुणों के आधार पर किया जाता है।एक उत्पादन प्रणाली के रूप में, हम फ़ीड छर्रों की बाहरी गुणवत्ता से संबंधित चीज़ों के संपर्क में अधिक आते हैं।उत्पादन के दृष्टिकोण से, जलीय फ़ीड छर्रों की गुणवत्ता को प्रभावित करने वाले कारकों को मोटे तौर पर निम्नानुसार संक्षेपित किया जा सकता है:
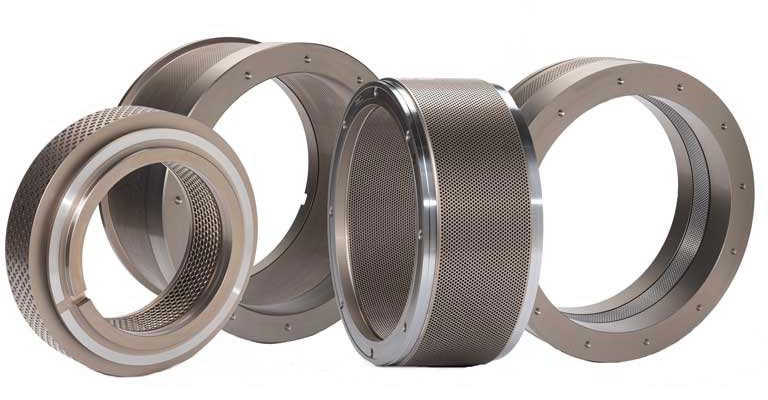
(1) सूत्रों के डिजाइन और संगठन का जलीय फ़ीड छर्रों की गुणवत्ता पर सीधा प्रभाव पड़ता है, जो कुल का लगभग 40% है;
(2) कुचलने की तीव्रता और कण आकार की एकरूपता;
(3) रिंग मोल्ड का व्यास, संपीड़न अनुपात और रैखिक वेग कणों की लंबाई और व्यास पर प्रभाव डालते हैं;
(4) रिंग मोल्ड का संपीड़न अनुपात, रैखिक वेग, शमन और तड़के का प्रभाव, और कणों की लंबाई पर काटने वाले ब्लेड का प्रभाव;
(5) कच्चे माल की नमी की मात्रा, तड़के का प्रभाव, शीतलन और सुखाने का तैयार उत्पादों की नमी की मात्रा और उपस्थिति पर प्रभाव पड़ता है;
(6) उपकरण स्वयं, प्रक्रिया कारक, और शमन और तड़के के प्रभाव कण पाउडर सामग्री पर प्रभाव डालते हैं;
3. प्रबंधन के उपाय:
(1) कपड़ा खुरचनी की लंबाई, चौड़ाई और कोण को समायोजित करें, और घिसे हुए खुरचनी को बदलें।
(2) छोटी फीडिंग मात्रा के कारण उत्पादन की शुरुआत में और अंत में काटने वाले ब्लेड की स्थिति को समय पर समायोजित करने पर ध्यान दें।
(3) उत्पादन प्रक्रिया के दौरान, स्थिर फीडिंग दर और भाप आपूर्ति सुनिश्चित करें।यदि भाप का दबाव कम है और तापमान नहीं बढ़ सकता है, तो इसे समय पर समायोजित या बंद किया जाना चाहिए।
(4) बीच के अंतर को यथोचित रूप से समायोजित करेंरोलर खोल.नए रोलर्स के साथ नए सांचे का पालन करें, और घिसाव के कारण प्रेशर रोलर और रिंग मोल्ड की असमान सतह की तुरंत मरम्मत करें।
(5) रिंग मोल्ड के गाइड छेद की मरम्मत करें और अवरुद्ध मोल्ड छेद को तुरंत साफ करें।
(6) रिंग मोल्ड का ऑर्डर करते समय, मूल रिंग मोल्ड की अक्षीय दिशा के दोनों सिरों पर छेद की तीन पंक्तियों का संपीड़न अनुपात बीच की तुलना में 1-2 मिमी छोटा हो सकता है।
(7) जितना संभव हो सके तेज धार सुनिश्चित करने के लिए 0.5-1 मिमी के बीच नियंत्रित मोटाई वाले नरम काटने वाले चाकू का उपयोग करें, ताकि यह रिंग मोल्ड और प्रेशर रोलर के बीच मेशिंग लाइन पर हो।
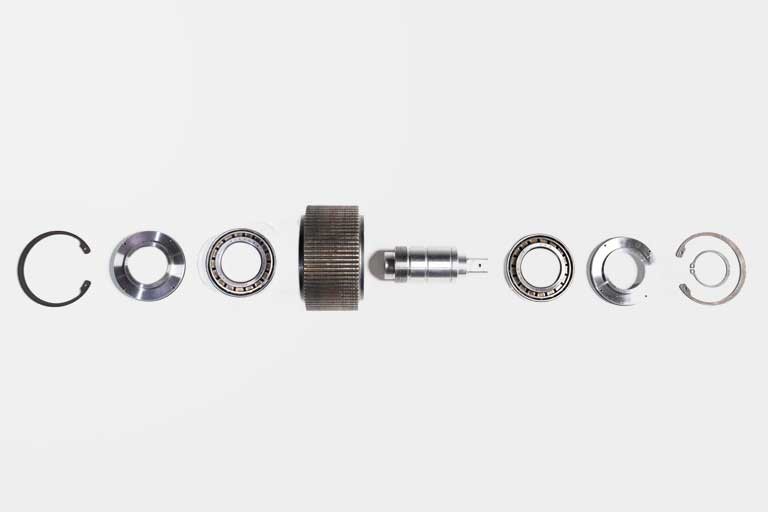
(8) रिंग मोल्ड की सघनता सुनिश्चित करें, नियमित रूप से ग्रेनुलेटर के स्पिंडल क्लीयरेंस की जांच करें, और यदि आवश्यक हो तो इसे समायोजित करें।
6、 सारांश नियंत्रण बिंदु:
1. पीसना: पीसने की सुंदरता को विशिष्ट आवश्यकताओं के अनुसार नियंत्रित किया जाना चाहिए
2. मिश्रण: उचित मिश्रण मात्रा, मिश्रण समय, नमी की मात्रा और तापमान सुनिश्चित करने के लिए कच्चे माल के मिश्रण की एकरूपता को नियंत्रित किया जाना चाहिए।
3. परिपक्वता: पफिंग मशीन का दबाव, तापमान और नमी को नियंत्रित किया जाना चाहिए
कण सामग्री का आकार और आकार: संपीड़न मोल्ड और काटने वाले ब्लेड के उचित विनिर्देशों का चयन किया जाना चाहिए।
5. तैयार फ़ीड में पानी की मात्रा: सुखाने और ठंडा करने का समय और तापमान सुनिश्चित करना आवश्यक है।
6. तेल छिड़काव: तेल छिड़काव की सटीक मात्रा, नोजल की संख्या और तेल की गुणवत्ता को नियंत्रित करना आवश्यक है।
7. स्क्रीनिंग: सामग्री की विशिष्टताओं के अनुसार छलनी के आकार का चयन करें।
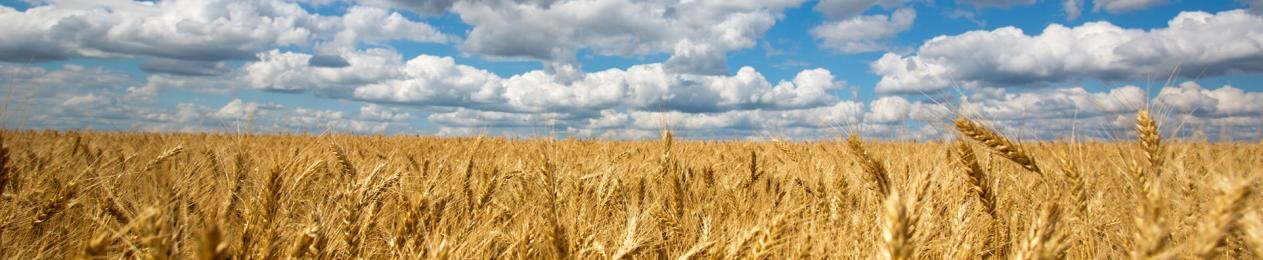
पोस्ट करने का समय: नवंबर-30-2023